What is supply chain due diligence?
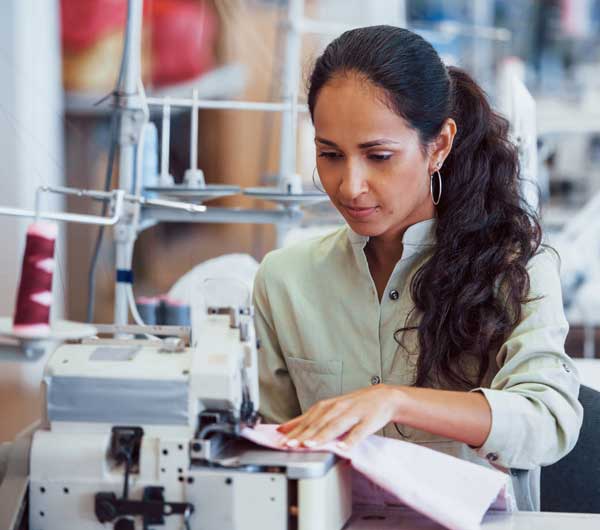
In short, a company is responsible for protecting human rights and the environment - throughout its supply chain. This requires the company to look beyond its own operations to its (direct and indirect) business partners.
Due diligence requires taking structured actions, including:
- Regularly analyzing, prioritizing and disclosing risks
- Building policies and mechanisms for prevention
- Promptly mitigating and addressing adverse impacts
- Providing channels for all stakeholders to receive information and to report issues (without retribution)
- Publicly communicating the existence, policies, solutions and mechanisms for all of the above
Due Diligence Laws and Frameworks
Laws
Frameworks
Webinar
Due Diligence Laws
- US Fashioning Accountability and Building Real Institutional Change Act (FABRIC Act) - Pending
- New York Fashion Sustainability and Social Accountability Act (Fashion Act) - Pending
- California Transparency in Supply Chains Act
- California Garment Worker Protection Act
- European Corporate Sustainability Due Diligence Directive (EU-CSDDD)
- German Supply Chain Act (LkSG)
- UK Modern Slavery Act
- French Vigilance Act
- Dutch Child Labour Due Diligence Act
- Norwegian Transparency Act, etc.
First Steps for Corporate Due Diligence Compliance
Understand Your Supply Chain
- What are our main products?
- Do we know our suppliers - and their suppliers - in our supply chain?
Define Requirements
- Include due diligence risk indicators in your supplier information
- Include clause for adhering to human rights and environmental standards
- Reach out and collaborate with suppliers - Offer support for implementing your requirements and working toward more sustainable production
Solutions for Corporate Due Diligence in Supply Chains
Customized Support
Analysis
Certification
You're not alone.
We offer:
- Tailor-made solutions for due diligence in supply chains:
Together, we develop practical and realistic measures with a strategy tailored to your company. - Project support:
We support you in creating conditions, policies and communications, and implementing them in your supply chains. Through our global network, we provide world-class, local support.
Missing Pieces
We offer:
- Status:
In a joint workshop, we shed light on your business activities to obtain a supply chain status quo. - Gap Analysis:
Together, we identify possible gaps in your sustainability concept and define a roadmap, roles and responsibilities for targeted implementation.
OEKO-TEX® RESPONSIBLE BUSINESS & Green Button
These certifications are the next step for the practical implementation of due diligence obligations.
- OEKO-TEX® RESPONSIBLE BUSINESS
A management tool for implementing corporate due diligence along your supply chains - Hohenstein is an OEKO-TEX® founding member.
or
- Green Button 2.0
The German government seal for sustainable textiles that requires compliance with corporate due diligence as one of the two pillars - Hohenstein is a certification body approved to award the Green Button label.
Due Diligence Laws Affecting Textiles
New York Fashion Environmental Accountability Act (NY Fashion Act)
What/Who
Indicators
Requirements
Enforcement
This legislation would require companies to:
- Disclose sustainability and due diligence activities
- Report on actual and adverse impacts
- Map their supply chains
- Take action to address human rights and environmental risks in their operations and supply chains
Applies to Fashion Companies that:
- Manufacture, sell or market apparel, footwear and/or fashion bags
- Conduct business in New York state (regardless of headquarters location)
- Have annual global gross receipts >100 million USD
Exceptions:
- Multi-brand retailers—unless private label fashion sales exceed 100 million USD
- Online platforms with less than 50% of total sales from apparel, footwear or fashion bags
Due Diligence Indicators
- Carbon emissions
- Chemical use/stewardship
- Collective bargaining
- Deforestation
- Exploited, forced and child labor
- Water footprint
- Wastewater
- Worker wages
Main Requirements of the NY Fashion Act
- Supply Chain Mapping
- Take a risk-based approach
- Trace and map suppliers across all tiers of production
- Tier 1 - Minimum 85% by volume - within 12 months of effective date
- Tier 2 - Minimum 75% by volume - within 2 years
- Tier 3 - Minimum 55% by volume or dollar value – within 4 years
- Tier 4 - Minimum 75% by volume or dollar value - within 6 years
- Disclose suppliers: Name, address, parent company, product type, number of workers at each site, by country
- Mandatory Due Diligence
- Effectively identify, cease, prevent, mitigate, account for and remediate
- Actual and potential adverse impacts to human rights and the environment
- For all categories of harm
- In own operations and supply chain
- Reduce climate emissions - in own operations and supply chain - to align with levels of the Paris Agreement and Greenhouse Gas (GHG) Protocol
- Use science-based targets (SBTs) as the minimum standard for companies below 1 billion USD and absolute reduction for companies above 1 billion USD
- Include upstream, company and downstream activities in the scope
(e.g. providing incentive and assistance to supply chain partners for improved performance by embedding responsible purchasing practices) - Annually report previous year's GHG emissions inventory, with independent verification at least every other year
- Measurably improve the lives of garment workers
- Work with significant mill partners to:
- Meet internationally recognized methodologies for chemical management and wastewater testing
- Effectively manage chemical use
- Effectively identify, cease, prevent, mitigate, account for and remediate
- Targeted Impact Reduction
- Quantify baseline and short-/long-term reduction targets on greenhouse gas emissions
- Remediate non-compliance with these emissions targets (within 18 months)
- Disclosure
- Reports available on the company website (readily available and free to access)
- Include any adverse impacts and reduction targets
- Submit annual, independently verified reports to the NY Attorney General, including labor records from suppliers throughout the supply chain
- Mean wages of all workers
- Comparisons to local minimum and living wages
- % unionized factories
- Weekly hours worked by month
- Overtime by company and country
Enforced by New York Attorney General
Penalties:
- Companies have 3 months to remediate noncompliance
- After 3 months, fines up to 15,000 USD per day
Failure to comply includes:
- Failure to conduct due diligence
- Failure to conduct due diligence in an effective manner
Regardless of due diligence conducted, each party involved will have independent liability to garment workers for any lost wages.
U.S. Fashioning Accountability and Building Real Institutional Change Act (FABRIC Act)
What/Who
Requirements
Penalties
Goal:
- Protect American garment workers (conditions, pay)
- Favor domestic manufacturing with good working conditions
- Increase accountability for brands and retailers to protect workers
Includes:
- Any form of preparation of a garment or section or component of a garment, cutting, sewing, making, processing, repairing, assembling, dyeing, pressing, altering, changing garment design, adding labels, final alterations or causing another person to do these actions
- Designed for or intended to be worn by an individual, which is to be sold or offered for sale or resale
- All layers of garment contracting (regardless of tiers)
Requires manufacturers, contractors and brand guarantors to:
- Pay hourly rate of at least minimum wage (instead of per piece rate)
- Keep records - TBD
- Certificate of registration from the Department of Labor - Federal Garment Factory Registry
- Within 6 months of contract for manufacturing
- Annually thereafter
- Posted and accessible by any employee during the work day
Noncompliance results in:
- For any companies that pay at price rate and manufacturers who contract with them
- Up to 50,000,000 USD, depending on:
- Size of the business
- Whether the violation was committed in good faith
- Gravity of the violation
- Any previous violations
- History in complying with the recordkeeping requirements
California Transparency in Supply Chains Act
What/Who
Requirements
This law requires public disclosure regarding verification, audits, certification, accountability and training. It does not require any actions, only transparency as to the extent (or lack of) company's efforts with regard to protecting labor within their supply chains.
Affects:
- Retailers or manufacturers
- Doing business in California
- With annual worldwide gross receipts >100,000,000 USD
Required Disclosure
Regarding the extent - or lack - of efforts throughout supply chain for:
- Verification to evaluate and address risks of human trafficking and slavery (with specification if not conducted by 3rd party)
- Supplier compliance audits (with specification if not conducted by 3rd party)
- Any certification required of direct suppliers that materials comply with labor laws in their country or encouragement to comply with all relevant laws
- Internal accountability standards and procedures for employees or contractors failing to meet company standards
- Provided training on mitigating risks within supply chains
California Garment Worker Protection Act
What/Who
Requirements
Penalties
Goal: Fair wages for garment workers in California
Includes:
- Work in garment manufacturing, cutting, sewing, making, processing, repairing, assembling, dyeing, altering, changing garment design, adding labels, final alterations or causing another person to do these actions
- All layers of garment contracting (regardless of tiers)
Allows: Garment workers to seek damages for work they have already completed
Requires manufacturers, contractors and brand guarantors to:
- Pay hourly rate of at least California's minimum wage (instead of per piece rate)
- Keep worker details and pay records for 3 years
- Keep contracts, invoices, orders, style sheets, etc. for 4 years
- Register with the Labor Commissioner
Noncompliance results in:
- For any companies that pay at price rate and manufacturers who contract with them
- 200 USD/employee/pay period
European Corporate Sustainability Due Diligence Directive (EU-CSDDD)
What/When/Who
Enforcement
The law:
- Establishes a company's duty to end, prevent, mitigate and account for:
- Negative human rights and environmental impacts within its own business area, by its direct contractual partners, by other (indirect) suppliers
- Climate impacts per 2050 targets set by the Paris Agreement and intermediate targets established by European Climate Law
- Affects companies headquartered or active in the EU (and their global suppliers):
- EU companies with >500 employees and net worldwide turnover >150 million Euros
- Non-EU companies with EU turnover >150 million Euros
Compliance with the EU-CSDDD is supervised and enforced at the Member State level.
- Sanctions include fines, compliance orders for:
- Failure to comply
- Failure to identify, prevent or mitigate risks
- Civil liability - ability for victims to get compensation
UK Modern Slavery Act
What/Who
Requirements
The UK law makes companies responsible for ensuring compliance in their own operations and supply chains via reporting, transparency and due diligence.
Applies to companies with annual turnover of £36 million:
- UK companies and subsidiaries
- Commercial organizations (regardless of headquarters) doing business in the UK
Requirements for Companies
Risk Assessments
- In company's own operations, organization structure and global supply chains
- Supply chain mapping
- Identification of geographies and industry sectors with potential risks
- Supplier communication and annual questionnaires on operations with risks
Corrective Actions
- Maintain corrective actions system, policy and steps to eliminate banned practices
- Annual statement, including whistleblowing policy (with no repercussions)
Supplier Code of Conduct
- Based on International Labor Organization and United Nations Guiding Principles on Business and Human Rights
- Available to suppliers
- Include zero tolerance policy, working conditions and living wages
Supply Chain Due Diligence
- Staff training
- Proof of taking all necessary steps to identify and prevent slavery in own operations and supply chains
- Process for monitoring and enforcing consequences
Audits
- Supplier audits to identify non-compliance
- Investigations of potential risks or violations
- Communication of how audits are conducted
Annual Reporting
- To UK government within 6 months of company's financial year-end
- On company website
- Including:
- A human trafficking/modern slavery statement, including prevention steps taken
- Due diligence processes
- Risk assessment and management
- Key performance indicators on actions
- Staff training
German Supply Chain Due Diligence Act
What/When/Who
Risk Factors
Requirements
Enforcement
The German Supply Chain Due Diligence Act (or "Supply Chain Act") came into force in January 2023.
The law requires companies to implement defined due diligence obligations for respecting human rights and certain environmental requirements.
The law:
- Affects companies with headquarters, administration, statutory seat or branch in Germany
- 2023: Companies with >3,000 employees
- Starting 2024: Companies with >1,000 employees
- Indirectly requires suppliers and partners outside Germany to:
- Provide info on human rights and environmental standards in supply chains
- Meet minimum standards
- Makes the company responsible for any actions:
- Within its own business area
- By its direct contractual partners
- By other (indirect) suppliers
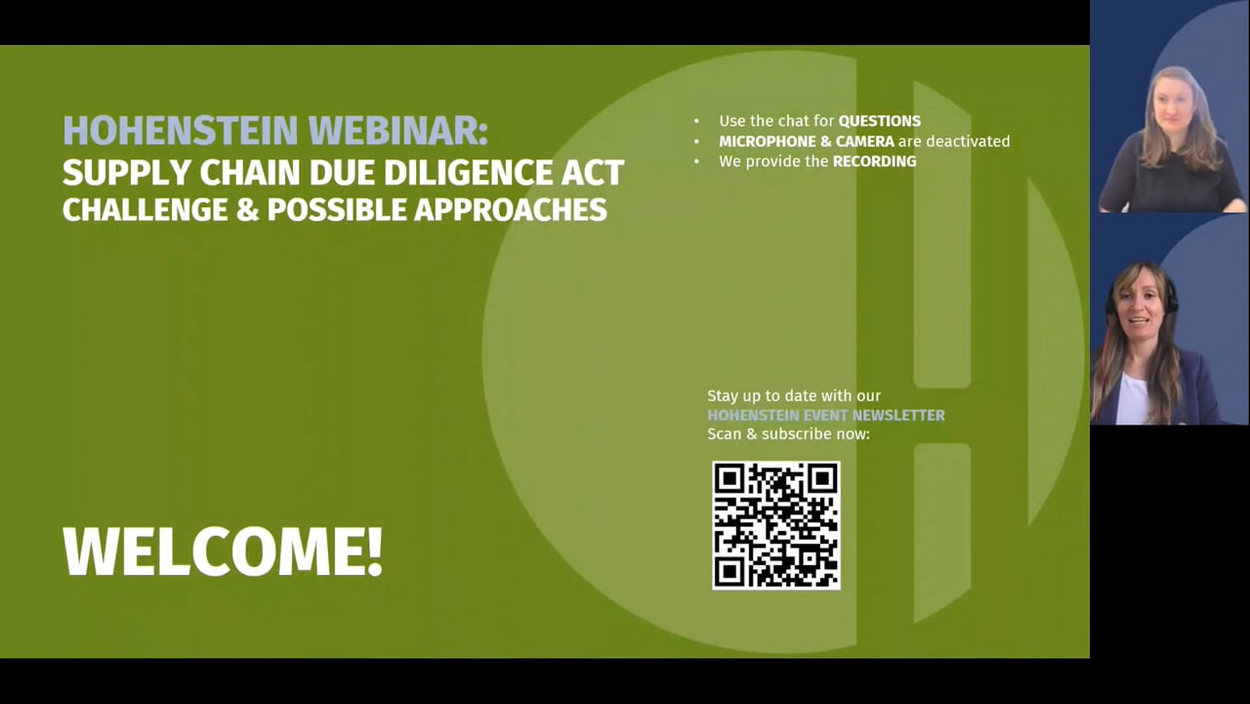
Due Diligence Risk Factors and Duties
Human Rights
- Child labor
- Forced labor
- Slavery
- Occupational health and safety
- Freedom of association
- Equal treatment at work, including equal pay
- Reasonable wage
- Harmful environmental changes that can significantly affect people
- Land grabbing
- Excessive use of force by security forces
- Other manifestly unlawful conduct that may directly affect human rights in a particularly serious manner
Environmental
- Mercury
- Persistent Organic Pollution
- Dangerous waste
What does the German Supply Chain Act require of companies?
- Determine internal responsibilities
- Establish a risk management system
- Conduct regular risk analyses
- Issue and publish a policy statement
- Establish preventive measures
- Establish and implement corrective measures for any violations
- Establish a complaints procedure
- Document and annually report on supply chain management
Compliance with the German Supply Chain Act is monitored and enforced by the German Federal Office of Economics and Export Control (BAFA). Its tasks include:
- Checking compliance with reporting obligations
- Conducting inspections
- Detecting, eliminating and preventing violations
- Imposing coercive sanctions and fines